Welding machine purchasing advice: how to choose the right product
- The most important in a nutshell
- Welding equipment is used to join metallic workpieces together.
- The most common processes are electrode welding and gas-shielded welding.
- An electrode welder is easy to use, but inaccurate.
- When welding, it is essential to protect the eyes.
When metals fuse together
If you work with metal, you can’t avoid welding for certain projects. Welding is the most important process for permanently joining metals. The workpieces are melted at the designated points and joined in this way. Welding technology is not only used for steel girders. The areas of application are as diverse as the metals themselves. Many everyday objects are made of metal, such as chairs with a steel frame. Anywhere a weld can break, the problem can be fixed with the help of a welder.
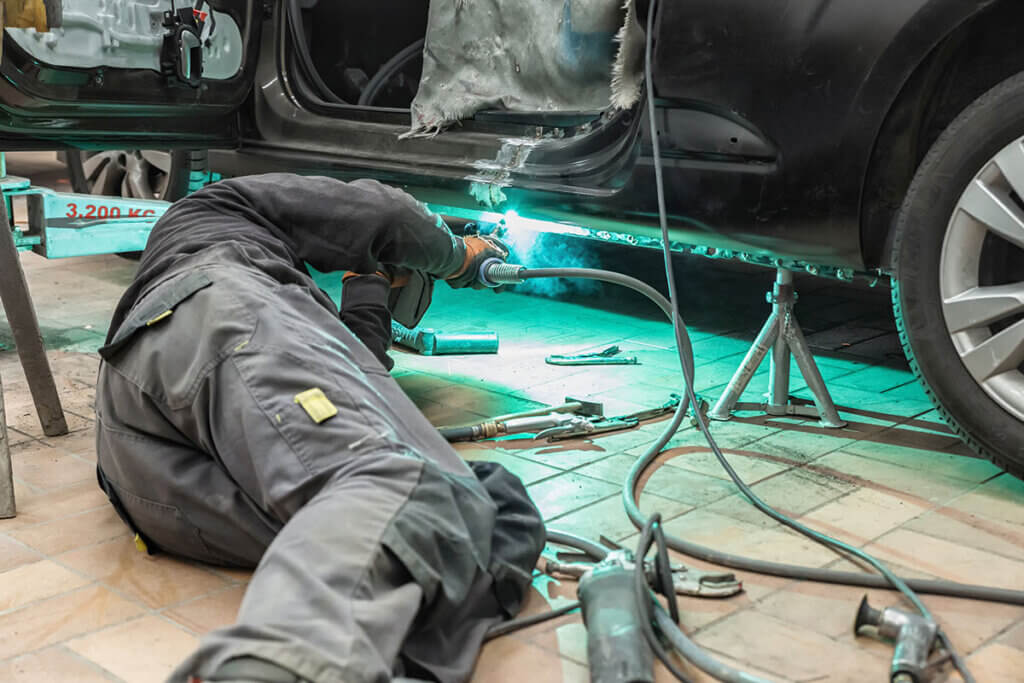
What are the welding processes?
Before buying a welding torch, it is important to familiarize yourself with the most common welding methods. Most welding equipment is capable of only one welding process. Which machine is the right one depends on the planned work.
Electrode welding – for simple work
Electrode welding is mainly used for light maintenance and repair work and is especially popular with do-it-yourselfers. It is the only welding method that works outdoors, since no shielding gas needs to be supplied. Electrode welding is also known as arc welding or electric welding. Almost all weldable materials can be welded with this method: These include, for example, boiler steel, tubular steel, stainless steel and cast steel.
In electrode welding, a rod electrode is held against the workpiece to be machined. For a fraction of a second, a short circuit occurs between the two poles, igniting the arc between the electrode and the workpiece, thus welding them together. This produces slag, which can be removed with a slag hammer after cooling. This welding process is suitable for all types of steel and stainless steel, but not for aluminum. There are various interchangeable electrodes for electrode welders, which are of different sizes and suitable for different materials.
Electrode welding is quick and easy to learn, making it ideal for small repair jobs. In addition, this method can be used in a wide variety of ways, as it allows any type of weld. Not every welder can weld overhead, for example. Electrode welders are also relatively small, easy to operate and robust. The bottom line is that this makes them ideal for beginners.
Advantages
- Outdoor welding possible
- Any welding position realizable
- Suitable for many metallic materials
- Handy
- Cheap
- Quiet
Disadvantages
- Rough method
- Slow
- Smoke development
TIG welding – professional welds
Tungsten inert gas welding, or TIG, is a relatively slow welding process, but one that can produce high-quality welds. This method is a form of gas shielded arc welding. This gas has the task of protecting the workpiece. Depending on the material, a different gas is used. During welding, it is used to protect the seam from direct contact with nitrogen, oxygen, hydrogen and dirt particles. These would affect the quality of the weld. The shielding gas therefore creates the conditions for good and clean work.
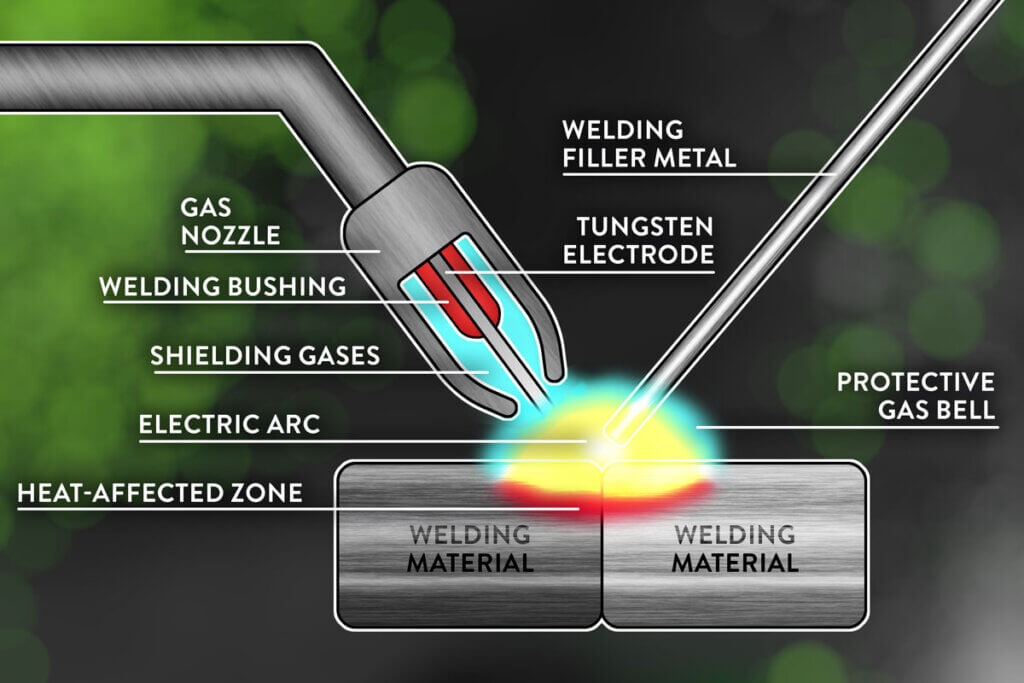
TIG welding is considered the most difficult welding process, because it usually requires two hands . The welding torch is held in one hand, while the other is used to add the filler metal to the molten pool created during welding. This is necessary because the tungsten electrode is very temperature resistant and does not melt off. The filler metal consists of an alloy similar to the materials to be welded and is melted. The feed is usually in the form of rods or wires.
TIG welding is suitable for stainless steel, aluminum and nickel alloys, and thin sheets of aluminum and stainless steel. The process is used wherever thorough and precise welds are required, for example in car restoration, furniture manufacturing or aerospace.
Advantages
- Suitable for fine work
- High quality seams
- No splashes
- All welding positions possible
- Welding of all fusible metals
Disadvantages
- Much experience required
- Slow
- Only suitable for thinner workpieces
- Expensive
MIG/MAG welding – for high workloads
MIG/MAG welding is commonly referred to as gas metal arc welding. A distinction is made between metal inert gas welding (MIG) and metal active gas welding (MAG). Gas-shielded metal arc welding enables particularly high working speeds. MIG and MAG welding differ only in the type of shielding gas used, which is inert or active. Since the welding process is the same, both variants are considered as a single welding process.
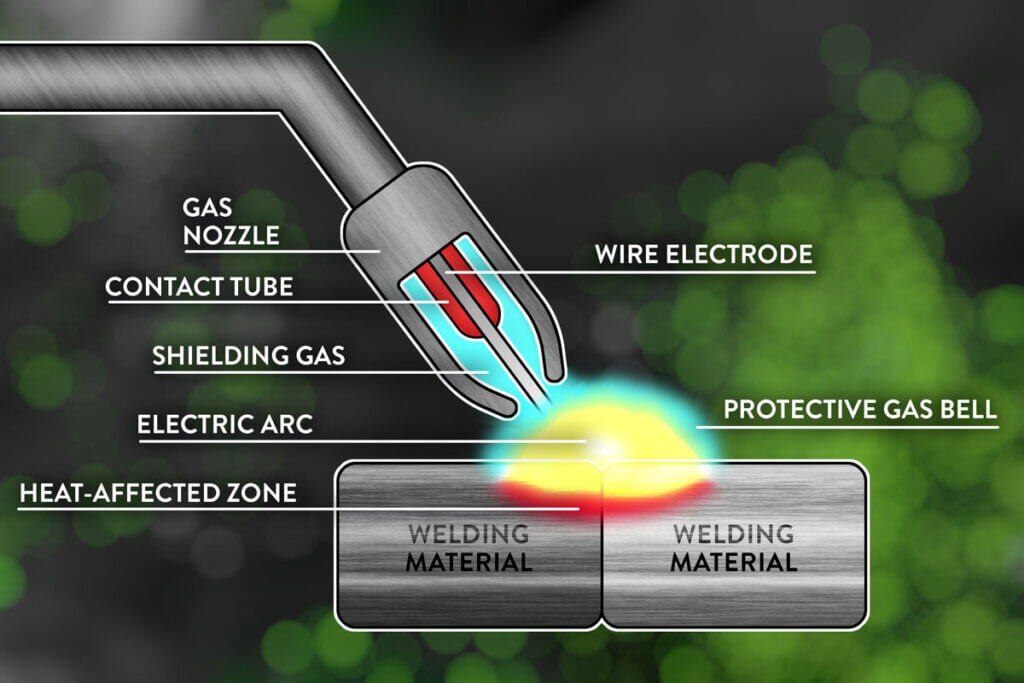
Compared to TIG welding, the MIG/MAG process has the advantage that the welder does not have to worry about the filler metal, as the welding wire comes out of the welding torch automatically and continuously at a selected speed. The MIG/MAG process is correspondingly fast and is particularly suitable for welding larger surfaces. For this reason, it is also frequently used in the metal industry. It has a wide range of applications: From motor vehicle production to steel and metal construction to apparatus engineering. Anyone who often has to weld something is well advised to use such a device. Since there may be problems with maintaining the shielding gas in outdoor areas or in drafty halls, a MIG/MAG unit is rather not recommended for outdoor use.
Advantages
- Easy to learn
- Quick
- Suitable for many materials
- Automatic wire feed
Disadvantages
- Conditionally usable outdoors
- Many splashes
- High acquisition costs
Multiprocess welder – the all-rounder
We talk about a multi-process device when the welder can perform several processes at the same level. Many designs master two procedures, but the secondary procedure only with cutbacks. This is due to the fact that, for example, the technical conditions of the MIG/MAG process allow the device to be equipped with the electrode welding process as well. The same applies to electrode welding and the TIG process. There is no talk of a “real” multiprocess unit until it is capable of welding all three processes at approximately the same level. Only then is there real added value for users.
A multiprocess welder is particularly interesting for frequent weldersdue to its flexible applicability. No matter what welding task is at hand, this device can handle it safely. In addition, the purchase of a single multiprocess device is significantly cheaper than buying three different devices. However, in order for the multiprocess welder to remain reasonably compact, extra functions are often omitted.
Advantages
- Flexible process selection
- Many materials coverable
- Cheaper than buying three devices
Disadvantages
- Partial functional compromises
- Large device
What to look for when buying
Due to the various welding processes, it is difficult to formulate universally applicable purchasing criteria for welding equipment. Since the devices are specialized for different processes, they have different functions and features. Nevertheless, there are some basic tips that will help when buying a welding machine.
Duty cycle or duty cycle
The duty cycle indicates how long a welding torch can be used. It is often referred to as the duty cycle. Welding equipment can only be used for a few minutes at a time because it shuts itself off to prevent overheating. So the length of the working cycle says everything about the performance of a welder. The cycle is given as a percentage and describes how long the device can be used within an interval of ten minutes.
Ten-minute welding is possible with a duty cycle of 100 percent. For most users, a duty cycle of 60 percent is particularly relevant, since most welding jobs do not take longer. In this case, welding can be performed for six minutes. After that, the device must cool down for four minutes. 50 percent duty cycle means that users can weld for five minutes and then the unit has to cool down for another five minutes. At ten percent duty cycle, the welder can be used for just one minute before it has to cool down for nine minutes. The duty cycle of a device should be clearly stated by the manufacturer. If this is not the case, it is a reason for skepticism.
Welding power source
In welding, it matters whether the device draws direct or alternating current. Depending on the current source, a distinction is made between DC and AC welding. The former is used for welding steel, stainless steel and special materials such as titanium and nickel. It is usually done with a negatively poled tungsten electrode. The latter is used for welding light metals such as aluminum and magnesium.
So, before buying a welder, you must already decide what materials they want to process. This automatically limits the number of models that can be considered.
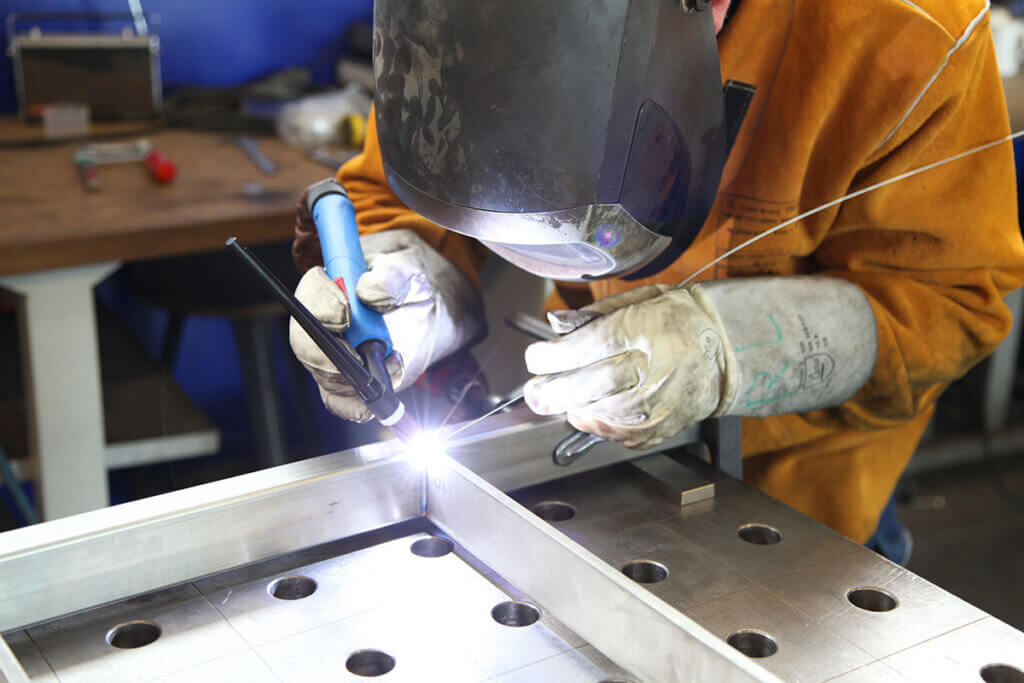
Synergy function
This function greatly facilitates the handling of a welding torch. Instead of synergy, there is often talk of automatic welding. Models with this function can be easily adjusted to the optimum. It is only necessary to enter the thickness of the material to be welded. The device then automatically sets the required amperage and voltage. This is particularly useful for beginners in the field of welding.
On some units with synergy function it is possible to store welding programs. This is very helpful when doing the same job over and over again. Basically, it should be said that the synergy function significantly simplifies the operation of the welder.
Notes on the use of a welding device
To weld successfully, the amperage on the unit must be set correctly. Otherwise, the arc cannot ignite. There is always some risk of injury when welding. Therefore, it is advisable to wear protective clothing. Eye protection in particular is essential.
Set current intensity
Before welding, the amperage on the welder must be set correctly. This is usually dependent on the thickness of the material to be processed. Rule of thumb: A power of 40 amperes is required per millimeter of steel. So for every additional millimeter, the power can be increased by 40 amps. To weld 10 millimeters of steel would require 400 amps of power. In the DIY sector, however, such a high amperage is not achieved in most cases. With such a high current carrying capacity, a welding torch could not be connected to the normal mains supply anyway. A power connection would be required for this.
Sockets for welding equipment
In principle, a welding machine can also be operated from the normal household socket. However, it is important to ensure that the socket has a fuse rating of at least 16 amps and that the welder is designed to operate at 230 volts. Ideal for operation is a three-phase socket, colloquially known as heavy or power current.
Depending on the type of welding equipment and the material to be processed, other parameters play a role in determining the correct amperage, for example the electrode diameter or, in the MIG/MAG process, the diameter of the welding wire. The best way to find out what to look out for is to consult the operating instructions for your welding equipment.
It does not work without ground terminal
One of the key elements in welding is the ground clamp, because before you start working, you need to establish proper grounding. This eliminates the risk of electric shock. During welding, grounding is established by means of a ground cable, which closes the circuit between the welding torch, workpiece and power source. The ground cable has a clamp on one end covered with copper strips, which is attached to the workpiece. It is important to keep the grounding point absolutely clean and free of rust, paint or other contaminants at all times.
Occupational safety during welding
Using a welding machine for a long time is a great physical strain. Working without the appropriate protective equipment is therefore anything but advisable. Anyone who welds for long periods of time must protect themselves accordingly.
Eye protection
In order to weld in a controlled manner, welders must constantly look into the arc. In the process, the eyes are exposed to radiationto an extent that is harmful to health. It is therefore essential to protect the eyes, either with a hand shield or a welding helmet. The latter is much more comfortable, as it leaves the welder with both hands free.
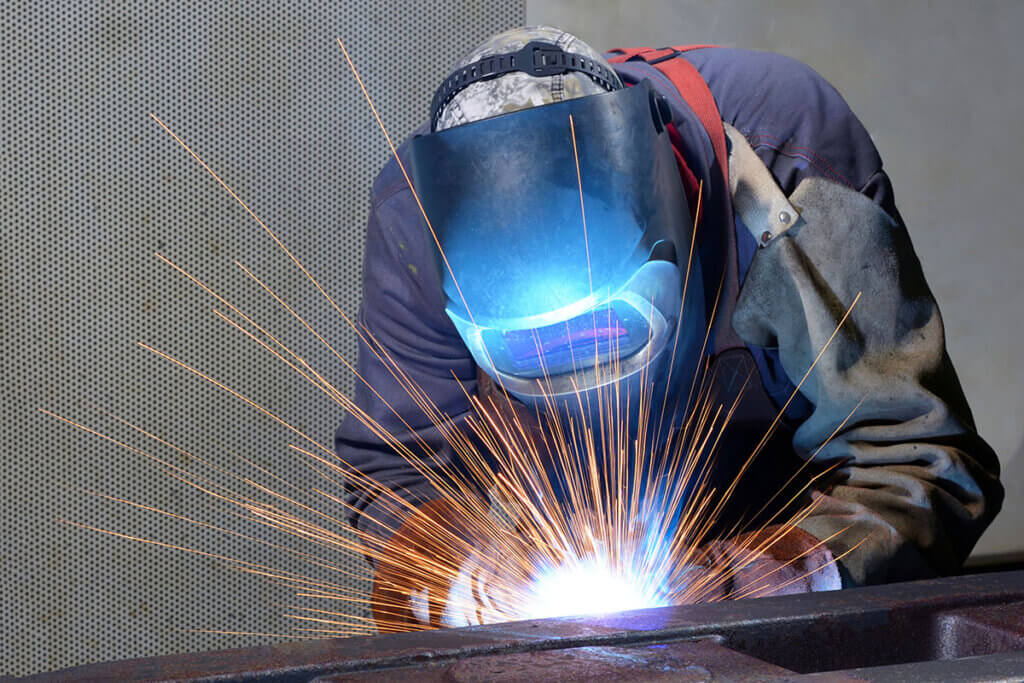
Anyone who accidentally looks into an arc unprotected for too long can suffer “flashing”. Everyone knows the unpleasant feeling of looking directly into the sun. The only difference is that the radiation of an electric arc is many times higher. During a short eye contact, the eye is blinded, but recovers quickly. However, if you look into an arc for a long time without protection, you will permanently damage your eyes. It varies from person to person how long the effects of “flashing” last. Those affected are extremely sensitive to light and prefer to keep their eyes closed. Ointments from the pharmacy and cooling help to relieve the pain. As a rule, the discomfort subsides after one to two days.
Respiratory protection
Smoke is always produced during welding. This smoke is a mixture of gases and small particles that are inhaled through the mouth and nose. According to studies, as many as 98 percent of the particles in welding fumes are smaller than 0.5 micrometers. This is referred to as alveolar dust, which can penetrate even the smallest branches of the lungs. Depending on the material and welding process used, adverse health effects range from respiratory irritation to cancer. Therefore, at least an FFP2 or FFP3 respirator should be worn during welding. Even better are professional solutions such as an air filter system in the welding helmet or a stationary extraction device at the workplace.
Protective clothing
One of the most common welding injuries is “welder’s neck” – a sunburn in the neck area caused by the high levels of UV radiation used in arc welding. Sparks and spatter can also give welders unpleasant burns, known in the jargon as “arc tattoos.” These injuries were not particularly dangerous, but still unpleasant and, above all, easily avoidable.
Protective clothing should be worn during any type of welding work, consisting of gloves and long-sleeved, flame-retardant clothing. It protects against sparks, splashes, heat, radiation and, above all, direct contact with the welding flame. It is important to always close the jacket or jumpsuit all the way up to cover as much skin as possible. The special protective clothing is divided into two levels. The lower level 1 is suitable for use in TIG welding. The higher level 2 is recommended for the MIG/MAG process.
Fig. 1: © JoFI / stock.adobe.com | Fig. 2-3: © Finalcheck | Fig. 4: © Jeanette Dietl / stock.adobe.com | Fig. 5: © industrieblick / stock.adobe.com