3D printer purchasing advice: how to choose the right product
- What you need to know
- 3D printers can produce highly precise models from various materials.
- They used to be extremely expensive, but now they are affordable for everyone.
- There are different production processes for different uses which cost different amounts.
- Some kits include only part of the printer. Additional components such as connectors can be produced by the printer itself.
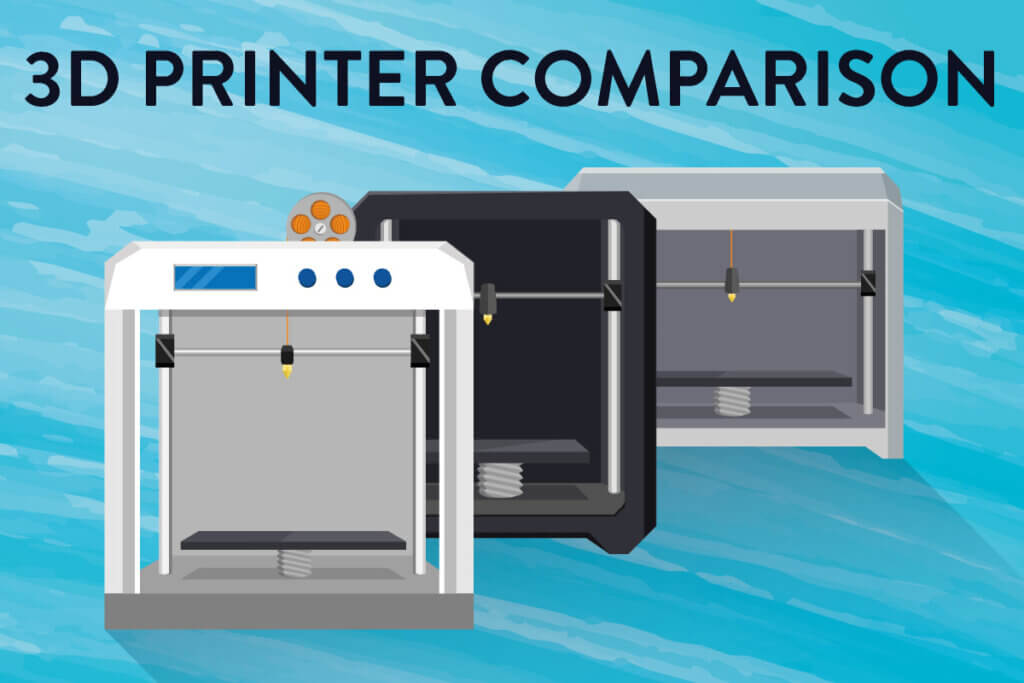
What is a 3D printer?
In the past, 3D printing was only a possibility for enthusiasts with a bulging wallet. Since then, the technology has become crucial in industry and medicine, and is also finding its way into more and more people’s hobby and tool rooms. Prices now start from under $250, making ownership possible for many.
3D printing is widely used in industry. The technology can be used to produce prototypes which are then tested, examined, and subsequently produced in series. In medicine, the technology plays an important role. For example, prostheses can be made with millimeter precision – useful for things like hip and jawbone replacements which need to be extremely precise. For hobbyists, 3D printing makes it possible to make spare parts, such as screws or other connecting parts, or to try out printing a specific object, such as an action figure or a flower vase.
With the right instructions, a 3D printer can reproduce almost any object in detail. Moreover, these printed models are infinitely reproducible. Compared to conventional methods, production time is shorter and individual production is cheaper. All you need apart from the printer and the printing material is a file with the building instructions – you can either measure and design one yourself or just download the files from the internet. The device will then print the model one-to-one according to this construction plan. The accuracy of 3D printers is extremely high: some models have a deviation of only 0.2%. As a result, true-to-scale production is possible – even with moving parts and in multi-colored versions.
Additive manufacturing (AM)
3Dprinting is also known as additive manufacturing (AM), and sometimes as rapid prototyping. The terminology is flexible depending on usage (e.g. industrial vs home) but what remains the same is that they refer collectively to manufacturing processes in which a liquid or solid raw material is formed or assembled into a three-dimensional object from a computer design. Heated and liquefied material is applied layer by layer via a nozzle in an injection chamber, gradually building up an object. Additive means that material is added and not removed, as you would find in milling or drilling.

Earlier technology: milling and injection molding
Milling and turning (e.g. with a lathe) are regarded as technical predecessors to 3D printing. These technologies are subtractive – they remove to create new objects. In this way, they are the inverse of 3D technology. A large blank is reduced in size by removal and the new object is shaped. Small parts can be fitted together to make large scale objects. In many ways, the process might be thought of as like sculpture.
A newer and more advanced form is injection molding, which is used to produce larger and more complex objects in one step. In this process, plastic is commonly used. It is heated and then pressed into shape using a negative. The prime example of a product made in this way is a Lego brick.
In a way, 3D printing is similar to injection molding. However, 3D printing does not require a negative. Rather, the digital 3D model is translated into machine-readable code and the construction is then built up layer by layer.
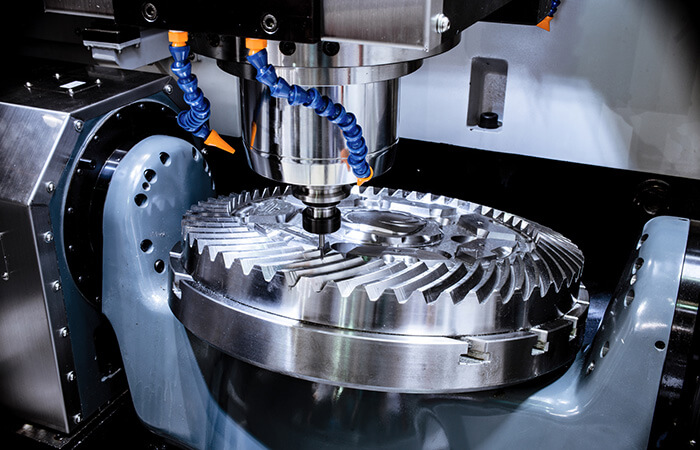
Industrial uses
In the past, industrial prototypes and model samples were produced manually using cardboard, foam, or clay. Nowadays, computer-controlled 3D printers take over this task as they are far cheaper and faster.
Other use areas
Whether in research or production, 3D printers are present in the following fields:
- Medicine (e.g. implants and prostheses, dentures, hearing aids, bio-printing)
- Scientific research (e.g. robotics, space)
- Fashion & jewelry (e.g. templates for rings, necklaces)
- Transport (automotive and aerospace lightweight parts)
- Food (still in development, potential for sustainability and food waste solutions)
Kit or preassembly?
There are 3D printer models available on the market that are already fully assembled, as well as those you have to assemble yourself. Both variants have advantages and disadvantages. The choice for or against either depends on how much freedom you want in customizing your printer.
3D printer kits
The obvious main advantage of DIY kits is that they are cheaper than pre-assembled 3D printers. Moreover, if you build your printer yourself, you get more flexibility when it comes to choosing additional components and personalizing the machine to your needs. This makes updating your printer with the latest parts much easier. The construction plans are generally always open source, so you can have a look before buying to see what you would be getting yourself in for. Some models, such as RepRap printers, can print their own components. The main disadvantage to building your own printer is that you’ll need a fair bit of technical knowledge to make it work.
RepRap
RepRap printers are special in that they are designed to be self-replicating – they build themselves and other printers. The abbreviation stands for ‘Replicating Rapid Prototyper’. The project started at the University of Bath, in 2005, with the goal to develop a low-cost 3D printer and has since developed into a global open-source community. The blueprints are under the GNU General Public License, a set of agreements that guarantee free redistribution. Because of this and the fact that the printer can produce many of its components itself as often as desired, RepRap devices are comparatively cheap.
3D printer kits are best for hobbyists and tinkerers with some previous technical experience. If you’ve never installed a circuit board or soldered a component on, we wouldn’t recommend buying one. This said, the price advantage is compelling. Compared to assembled devices, you can save up to $400. DIY kits can start from just over $100. The cheapest models usually consist only of a plastic frame. To keep costs down, most printers don’t come with attractive casing.
Advantages
- Cheaper than preassembled printers
- Repairable and upgradable
Disadvantages
- Technical skills necessary
- Less attractive designs
Complete models
Complete 3D printers come preassembled. This means that you’re directly getting a tuned final product with tailored software. In most cases, this is more user-friendly, as you can use your intuition to operate the printer unlike the programs for kit devices. However, pre-assembled components and designs can make upgrading the printer much more difficult. This means that printers can become obsolete comparatively quickly. Spare parts can usually only be obtained from the manufacturer and are often expensive. The same applies to repairs, which can only be carried out in specialist workshops.
You don’t need any technical knowledge to use a preassembled printer: simply unpacking it is enough to start printing. Depending on the model, prices range from $200 to well over $5000.
Advantages
- No complex assembly
- Sleek designs
Disadvantages
- More expensive than kits
- Usually not upgradable
Buying tips
Budget and intended use will determine what kind of printer you should buy. Different models will print using different techniques and give different quality results. Let’s go into the details of what you should be looking for:
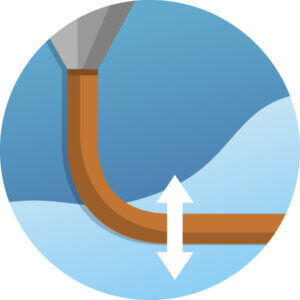
Print layer thickness
Print head thickness is usually between 0.02 and 0.2mm. If you want to make extremely detailed models, you will need a printer with an extremely small print head. The thinner this is, the less noticeable the individual printed layers will be in the finished model. Print layer thickness is reflected in price: the thinner the print head, the more expensive the printer.
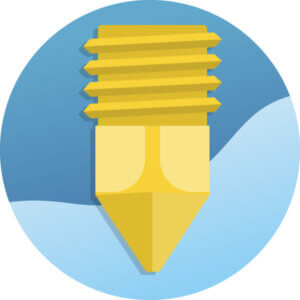
Extruder and nozzle
The extruder and the outlet nozzle (hot end) heat the material (for solid print materials). The unit ejects the material layer by layer via the nozzle. Most printers have only one extruder. For professional use, printers with two extruders are recommended, because they allow different materials to be printed simultaneously. This is very useful for printing support structures. For example, a water-soluble support material can be printed via the second extruder, which you can dissolve after printing is complete.
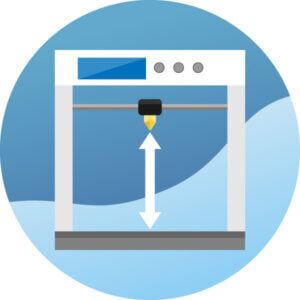
Build volume
The size of the build space determines the maximum build volume. The dimensions are labelled using an x-, y- and z-axis. Modern printers have a build volume anywhere between 10x10x10cm and 25x25x25cm. Printing volumes larger than this are currently still unaffordable for home use.
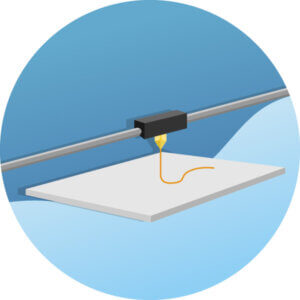
Print bed
The print bed is the surface on which the model is built. Depending on the printing process, the plate can be fixed or move in a horizontal or vertical direction. It is also important that the object adheres well during the printing process and that it can be removed easily after completion and cooling. Self-assembled printers make retrofitting a higher quality print bed very easy. You can even get heatable print beds now – these make it much easier to remove the model after it is finished.
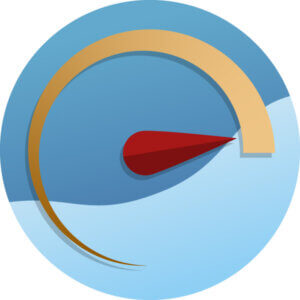
Print speed
Print speed (measured in mm per second) indicates how much printing material can be output in what time. Top of the range printers can reach 300mm/s, but these are not affordable for home users. Hobbyist-level devices generally achieve 50 to 100mm/s. Compared to industrial production, print speed is not generally a major issue for home use – waiting for a few hours for the model isn’t a big deal when you’re not running a production line. Besides the pure printing speed, curing time is also key.
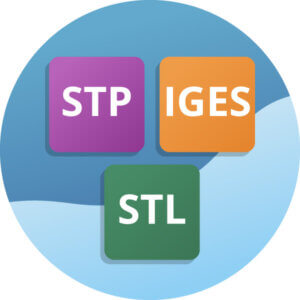
File formats
3D printers can process files that users have either created themselves in a CAD program or downloaded from the internet. However, three-dimensional files cannot be processed. To make these work, you have to convert 3D files into a file format that cuts the 3D model into 2D layers. These layers can then be printed together to make a model. Common file formats are: STP, IGES, STL, X3D, COLLADA, VRML (WRL), OBJ, PLY, AMF.
Printing methods: liquid and powder
There are various print technologies when it comes to 3D printing, each with their own advantages and disadvantages. Roughly speaking, you can categorize 3D printers through their use of materials in three different states:
- 3D printing with molten material
- 3D printing with liquid material
- 3D printing with powder
No matter which technique, 3D printers all need a file to print from, just like a normal paper printer. Based on the file, the machine moves the print head and extrudes the print material. To do this, the virtual three-dimensional model, usually contained in a CAD file, is divided into two-dimensional slices, so-called layers. This procedure is also called slicing. After the conversion, users receive a file in STL or AMF format. Using these kinds of files, the 3D printer then builds up the model layer by layer.
Some of the printing techniques only differ slightly. Some processes are often protected by patents and are specific to companies. Here are some of the available printing techniques:
Molten materials
The most common and cheapest method in 3D printing is the use of plastics such as ABS or PLA, which are melted and then applied in liquefied form layer by layer (free-space method).
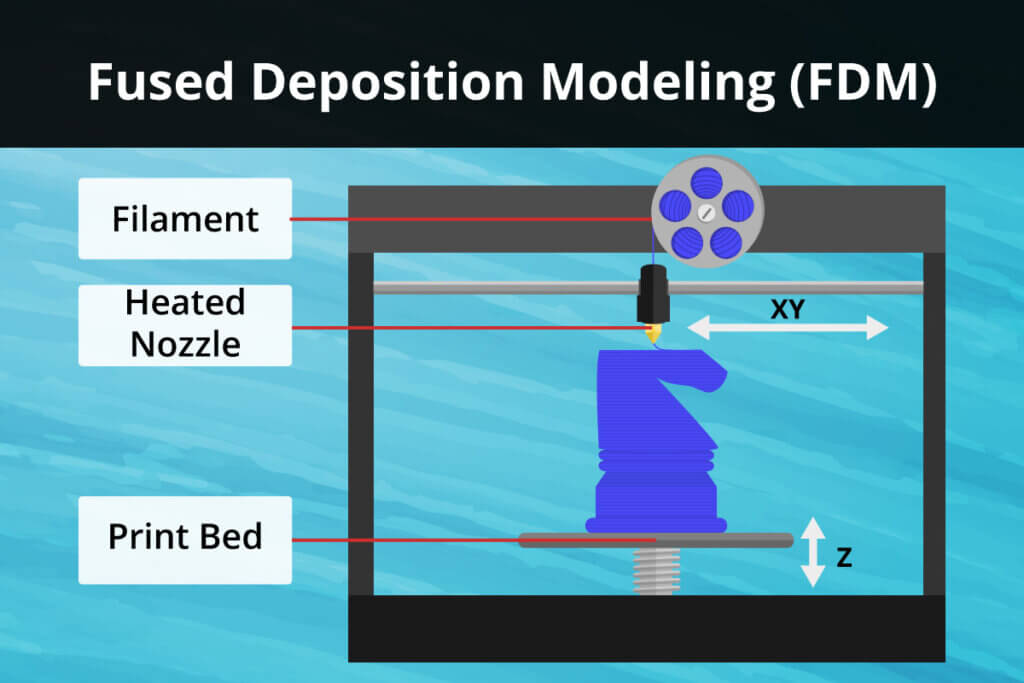
This process is called FDM (Fused Disposition Modelling) or FFF (Fused Filament Fabrication). FDM was developed in the USA and patented in 1989. Back then, FDM printers cost $10,000. When the patent expired in 2009, enthusiasts were able to copy the technology. Since the name was still patented, the new replica technology was called FFF. These replicas, often also referred to as RepRap devices, often do not have their own housing – they only have the minimum components necessary for printing. If you want to use multiple different filaments at the same time, then you’ll need multiple nozzles.
In principle, the whole process is like using a hot glue gun: a material is heated and ejected from a nozzle in a liquid state. The material then has to cool down in order to harden. Computer-controlled horizontal and vertical movements apply the filament to the desired areas. Only when one layer has cooled down can the layer above it be applied. Due to range of print materials and effect that different model shapes have, it is impossible to say generally how long such a printing process takes. Some models have a display which shows the calculated remaining time. These displays are also sometimes on preassembled printers.
Not just plastic
Other materials can be used instead of plastic in 3D printing, such as plaster, glass, or wood. With these different filament materials the usage scope expands – for example, with metal you can make medical splints and decorative items. People are even experimenting with foods like chocolate or mashed potatoes! However, in this case 3D printing is still currently too slow and too expensive for mass production. The best-known 3D printer manufacturers include Makerbot, Ultimaker, Flashforge, Creality 3D, Prusa and Geeetech.
3D printing with liquid material
This printing technology uses UV-sensitive liquid plastics called photopolymers. The liquid material technology has four different types:
Stereolithography (SLA or STL)
In a way, stereolithography is the predecessor of all 3D printing processes. It was patented as early as 1984 by the American Chuck Hull. This process is quite complicated and expensive as it is technically very sophisticated. In short, UV light is used to harden a special liquid plastic otherwise known as a photopolymer. The model is made in a container filled with the liquid photopolymer. To do this, the print bed is submerged in photosensitive liquid, just below the surface. Then, a laser irradiates the first layer, hardening it. Once this step is completed, the next layer can be produced.
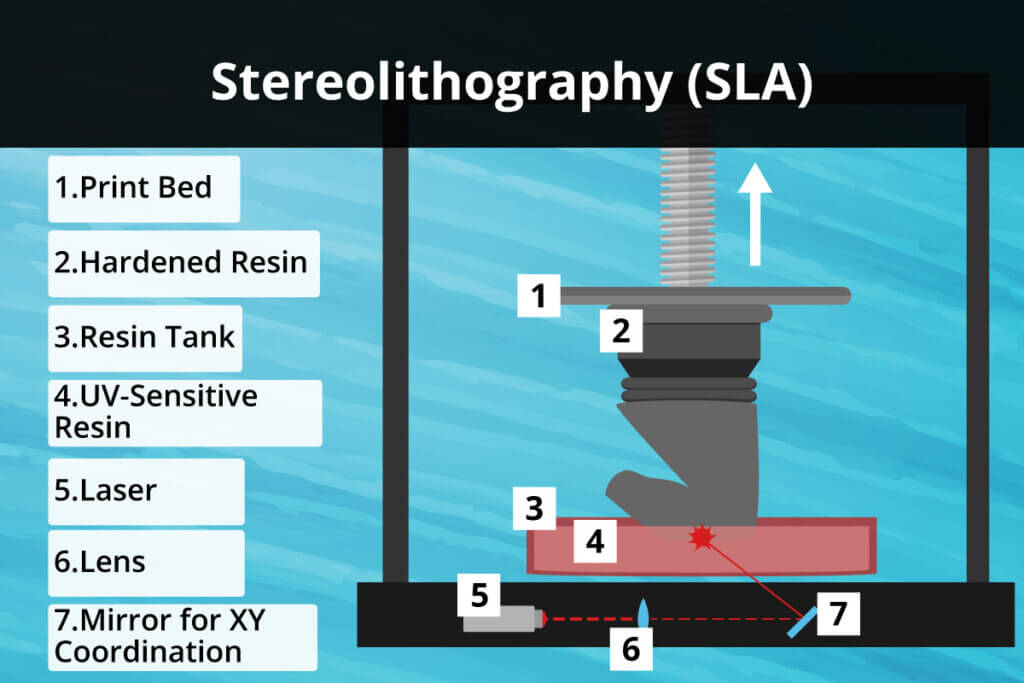
To create the object, the print bed moves down into the resin by exactly the thickness of a layer. The next layer is now hardened on the surface by laser application. This happens many times – it takes hours to assemble the millimetre-thick layers. In many cases, needle-like structures are necessary to support the object during printing, which are then broken off afterwards. They are made of the same material as the final product. It is also possible to mix the photopolymer with other materials such as ceramic. In this case, after successful printing, the ceramic object is fired. This gives the ceramic components a permanent bond and removes the plastic components.
Digital light processing (DLP)
This process works exactly like stereolithography. However, instead of a laser, a DLP projector is used as the light source. Sone printers can even use standard projectors.
MultiJet modelling (MJM)
MultiJet modelling, also known as PolyJet modelling, is a mixture of stereo lithography and the FDM technique. Here, a liquid and light-sensitive plastic is applied to the working platform via a print head. The mixture is then immediately hardened by a light source in the outlet nozzle.
Film transfer imaging (FTI)
The film transfer imaging process uses a similar light-based technique, here the material is cured with a projector. However, a transport film is used in this process. A film of the photosensitive material is applied to the transport film and then cured with light. Next, this cured layer is lifted from the film and joined to the rest of the workpiece. The process is repeated until all layers are complete.
3D printing with powder
There are in general two types of powder-based 3D printing, sometimes know as powder bed and inkjet or drop-on-powder printing. The powder is either melted or a binding material is deposited by an inkjet printer to form the object layer by layer. In both cases, the object is produced in a powder bed. The two processes are:
Selective laser sintering (SLS)
The term selective laser sintering (or laser melting) refers to the process in which three-dimensional objects are created by melting powder-like materials, such as plaster. Thin layers of powder are melted to form a 3D object. After a layer has solidified, a roller ensures that new powder is applied above the workpiece, which then sinters a new layer according to the computer file.
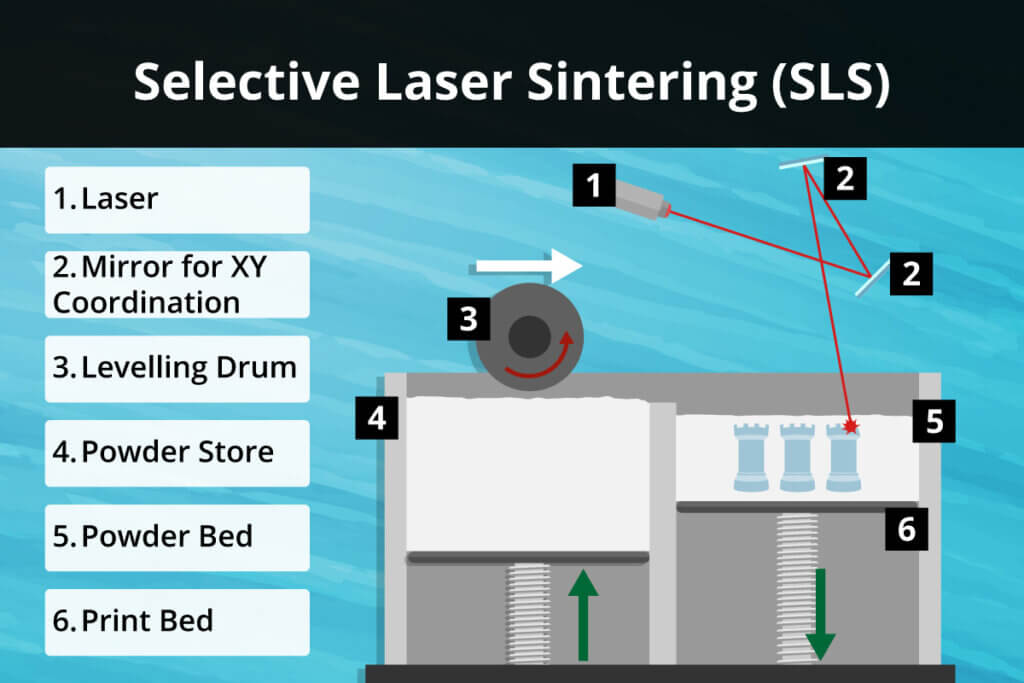
The individual layers are joined by the laser and the process is repeated until the model is finished. Excess powder is removed by suction and reused. Other materials that can be used are nylon, elastomers, alumides or polyamides. This method is comparatively expensive. Some materials still require finishing for cleaning or stabilization, for example with superglue.
3DP: adhesive bonding
In the 3DP process, powder is also used, but instead of being melted it is solidified with a liquid adhesive. This is applied via a pressure nozzle, just like ink in an inkjet printer. The assembled model then emerges these glued powder layers. Here, too, the working plate moves down a little before each new layer of powder is applied. Possible materials are plaster and plastic powders, ceramics, glass, and other powder-like materials. Like with the SLS technique, this process is extremely resource-efficient, as unbonded powder can be reused.
Printing materials: filament & pellets, powder, resin & wax
Depending on the printing technique you will need to use different printing materials.
Printing with liquid: filament or pellets
Extrusion refers to methods in which material is forced through a nozzle. In 3D printing, plastic filament or pellets are melted down to form a viscous liquid which can then be extruded before it hardens. The most common material used today is polyactide (PLA). It is a lactic acid-based plastic that is approved for use in the food sector as well as in the textile industry because it has no health risks. The fact that the material softens quickly is a further advantage for printing.
Since PLA is heat sensitive, even models which have cooled and hardened are sensitive to heat. Using this plastic for cups is an option, but only if you don’t put any hot liquid in them as they can deform. In fact, even direct sunlight and high room temperatures can affect a PLA 3D printed object’s structural integrity.
Acrylonitrile butadiene styrene copolymer (ABS) is less heat sensitive than PLA. However, it burns easier so you can get some unpleasant odors if this happens when you print.
The material you can use depends on the printer you have. Some 3D printers can only work with one kind of plastic. If your printer is capable of both plastics, in general it is best to use PLA as it is more eco-friendly and has a heat tolerance of 122 °F (50 °C). If you’re needing something which can withstand temperatures between 185 and 212 °F (85-100 °C), then ABS is the right option. If you’re looking for colored plastic, then color PLA (CPLA) is what you need – the plastic is mixed with ink meaning you can do multicolored printing.
Printing with liquid materials: PolyJet, resin, wax
In PolyJet printing, extremely small drops of a photopolymer are applied to the print bed and cured with the help of UV light. Instead of a photopolymer, synthetic resins and special waxes can also be used. At the end of production, the models are pulled upside down out of the liquid.
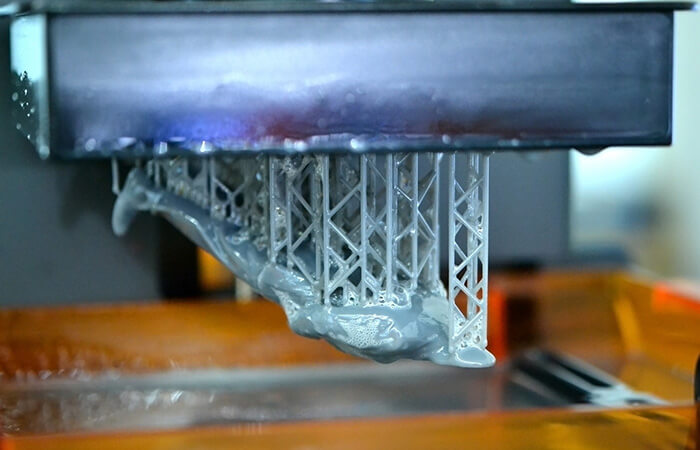
Printing with powder
3D printing with powder is still relatively expensive, due to the cost of the powder. The printing powder is either melted together by laser joined together via nozzles extruding special adhesives. Once the production of the model is complete, the excess powder can be removed with a brush or vacuum and reused.
Usage tips
So, you’ve decided to buy a 3D printer, but what now? The first thing to consider is where you install it. Read on for information about this as well as tips for creating computer models, printing objects, and cleaning.
Installation: location is key
Choosing the right location is essential, as it can have a big effect on print quality. Are you thinking of putting your printer on the floor, on a table, or on a workbench? If you’re considering the floor, you should know that dust accumulates most down there. When people walk through the room, they will stir up dust which can end up on the print bed. This can cause problems, especially if your printer doesn’t have a case. Dust can stop the model from adhering properly to the print bed, making it slip while printing. If you have dust on the filament, when it melts for printing it can clog the print nozzle.
Ventilation
Plastics like as ABS and PLA emit noxious vapors during melting, so installing your printer somewhere with good ventilation is essential. An extractor fan or at least good ventilation with fresh air is important to avoid any health risks from the fumes. This said, we don’t recommend using your 3D printer outside: any kind of wind will prevent adhesion. The motor and mechanics can be quite loud, so it’s best to put your printer away from living rooms and bedrooms.
How to print
After you’ve installed your printer in a suitable location, you now need computer-readable file. You can either create one yourself or download a model from the internet. If you’re new to 3D printing, then downloading a complete file is a great option to begin with. Save the file on an SD card or a USB stick so you can put it in the printer. Direct connections between computers and 3D printers aren’t common – it depends on the model, and in general isn’t that simple to set up for beginners. After heating the filament or pellets, printing can begin. If the model does not adhere to the print bed with the first layers, you’ll have to start again.
Post-processing & cleaning
After printing, some post-processing is necessary – which steps you need to take depend on the model and type of 3D printer you have. The model might have cool completely and harden, or you might have to brush or vacuum away any excess powder. Some models will need superglue or other stabilization to increase their structural strength. Depending on what you’ve made, you might also need to remove support structures – this can be done by hand with sandpaper, or with a liquid that dissolves the supports.
If your nozzle is clogged, you can unblock it by manually pushing some filament through the heating element. If this doesn’t work, try using a needle. In extreme cases you will have to disassemble the print head to clean it. Some models come with cleaning filaments to make sure there is no residue left behind.
When it comes to cleaning the print bed, make sure to only use special cleaning agents – if not, you can destroy the sensitive adhesive coating.
Image 1: © FinalCheck | Image 2: © xiaoliangge / stock.adobe.com | Image 3: © nordroden / stock.adobe.com | Images 4-12: © FinalCheck | Image 13: © mari1408 / stock.adobe.com